- 鋳造と鍛造の違い
- なぜ鍛造により、強くなるのか
- 鍛造の種類
- ホイール剛性の重要性
- リム部の製造方法
- 設計力
- 試験企画について
- BBS オフィシャルサイト
鋳造とは、アルミを高温で溶かし液状にして、それを型に流し込み、成型する手法。
メリットは、デザインに自由度があり、大量生産に向き、低コストでホイールが製造できること。
デメリットは、強度の問題から、ある程度の肉厚を確保しなければならないことから、
鍛造に比べて重量が重くなることです。
鍛造とは、大型のプレス機により、アルミに圧力をかけて、型に押し込み成型する手法。
メリットは、圧力をかけることから、アルミの金属粒子が緻密になり、強度が上がることから、
非常に薄い肉厚で製造でき、重量が軽く、剛性に優れます。
デメリットは、設備、型、加工とも非常に高価で、量産スピードが、鋳造より遅いことです。
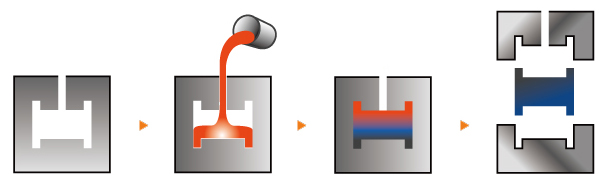
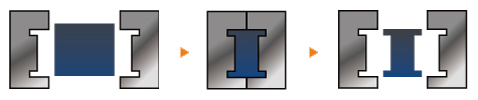
上記、製造方法の違いから、レーシングカーや、航空機のホイールは、鍛造により製造されます。
鍛造と鋳造のアルミ密度の違いは、ミクロ100倍写真にすると、一目瞭然です。
一般的な鋳造組織は、アルミの粒子が粗く、結晶がバラバラの方向を向き、パンのように荒くなっているのに対して、
BBSの鍛造組織は、餅のように緻密です。
一般的な鋳造アルミの粒子 | BBSの鍛造による粒子 |
![]() |
![]() |
このように、鍛造することにより、金属組織の粒子が緻密で均一となり、強度アップが図れるのです。
反対に、鋳造は、アルミの粒子が粗いだけではなく、熱収縮や空気の巻き込みによる、
特有の引け巣(アルミ粒子にエアが混入)が発生することから、強度にバラツキが出ることも、
デメリットのひとつとなります。
また、1c㎡あたりに、4トン以上の圧力をかけることにより、鍛流線(メタルフロー)と呼ばれる、
理想的な金属粒子の配列が生まれます。
![]() |
BBSの鍛流線(メタルフロー) |
この鍛流線が、荷重に対して、直角に近い角度で得られることによって、金属疲労強度が、
飛躍的に向上します。
結果、同じ強度を確保するのに、鋳造に比べて、鍛造は肉厚を薄くすることができ、
軽量/高剛性のホイールとなるのです。
一般的に、鍛造ホイールというジャンルの中の製品は、すべて同じ手法、同じ強さ、のように考えられていますが、
じつは、そうではありません。
一口に鍛造と言っても、その手法は、さまざま・・・。
各メーカーは、回転鍛造、融解鍛造、溶湯鍛造、裂開(レッカイ)鍛造等、鍛造技術にネーミングを付け、
差別化を図っています。
そんな中、BBS(ワシマイヤー社)が、行っている手法は、密閉鍛造。
簡単に説明すると、アルミの逃げ場をシャットアウトし、大きな圧力をかけて、アルミを押し潰す方式です。
この方式が、現在存在する手法の中で、一番、アルミの密度を上げることができます。
そして、強烈に密度が上がったときに、アルミ内部に、鍛流線と呼ばれるきれいな「線」ができるのです。
(密閉鍛造は、日本では、ワシマイヤー社のみが採用している技術です)
以前、GT500の開発テストで、BBS製ホイールと、他社製ホイールの比較テストを見たことがあります。
まったく同じタイヤを装着して、ホイールだけの比較テストを行っていたのですが、アウトラップもベストラップも、
すべてのラップでコンマ5秒、BBS製ホイールが速いという結果が出ました。
もちろん、BBS製ホイールの方が軽いというアドバンテージはあるのですが、ドライバーのコメントは、
加速やブレーキングといった、軽量によるメリットではありませんでした。
ドライバーは、「グリップに安定感がある」と言います。タイヤは、まったく同じなのに・・・・・。
この安定感の根源、それは、ホイール剛性によるものだったのです。
ブレーキング、トラクション、そしてコーナリングフォース(Gフォース)により、タイヤが変形するように、
ホイールも、タイヤの強力なグリップ力により、変形します。
では、下の図を見て下さい。
この変形(たわみ)は、車輌にホイールナットで装着されているハブ部(A)では、ほんの少しでも、
ハブから遠くなるに従って、大きくなります。特に、剛性の低いホイールでは、ハブ部から、一番距離のある、
リム部(C)は、大きく変形することになるのです。
もちろん、このリム部は、タイヤが装着されている部分であり、ここが変形することにより、
コーナーでタイヤを安定して接地させることができなくなってしまいます。
結果、コーナリング中、「グリップに安定感がある」 というコメントになるのです。
また、この変形は、ドライバビリティにも大きな影響を与えます。
なぜなら、高速コーナーをはじめ、ドライバーがミリ単位でステアリングを切ったとき、
ホイールが、勝手に変形し動いていたら、クルマは、ドライバーの意思どおり動いてくれないからです。
また、スポークやリムが変形すると、コーナーでタイヤを確実に接地させるために必要な、
キャンバー角をはじめとする、アライメントのセットアップも大幅に変わってくるのです。
では、キャンバーが付いている状態での、ホイールの断面図を見てください。
図からわかるように、特にリム部(C)では、ハブ部から距離があるだけではなく、
キャンバー角が付いていることから、かなり大きな力がかかります。
高剛性のBBSホイールは、ベースになる、ホイール全体の剛性を最大限まで引き上げるだけではなく、
このリム部(C)の剛性が、他社製品と比べて、圧倒的に高いことが、最大の特徴です。
結果、BBSホイールは、タイヤの接地面を確実に確保することから、ラップタイムを削り取り、
究極のドライバビリティを生み出すのです。
ホイールのリム部を製造する方法も、製造メーカーにより手法が違います。
一般的には、ホイールを回転させながら、ホットスピニングという方法にて、
暖めながら圧力をかけて、アルミを伸ばし、リム部を成型します。
対して、BBS(ワシマイヤー)では、スピニング時に、オイルにて摩擦で発生する熱を抑制し、
ホイールの熱を奪いながらリム部を成型する、コールドスピニング方式を採用しています。
コールドスピニングのメリットは、結晶流を粗大化させることなく、
緻密な鍛流線を細部にいたるまで、作り出せることです。
サスペンションスプリングの製造方法に、温間成型と冷間成型があるように、
リムの成型にも、温間と冷間があるのです。
もちろん、この技術は、BBS(ワシマイヤー)のみが使用できる、強度に優れる手法となります。
レーシングカーのフレーム補強(スポット溶接等)でも、補強が必要な場所は決まっています。
同様にホイールにも、強度/剛性の「キモ」になる部分が、数箇所あります。
BBS(ワシマイヤー)では、緻密な設計力によって、この強度が必要な部分をコントロールし、
最適な軽量と剛性バランスを実現しているのです。
BBS(ワシマイヤー)の製品は、VIAやJWLが取り決めている試験内容を、より過酷にして、
製品の規格検査を行っています。
たとえば、回転曲げ疲労試験では、規格回転数:10万回のところを、20万回以上。
半径方向負荷耐久試験においては、規格回転数:50万回のところを、100万回以上にて、テストを実施。
これらのテストをパスしないと、BBS(ワシマイヤー)の製品は、世には出ないのです。
まさに、高性能商品の裏付けです。